How to Choose the Right Packaging Machine

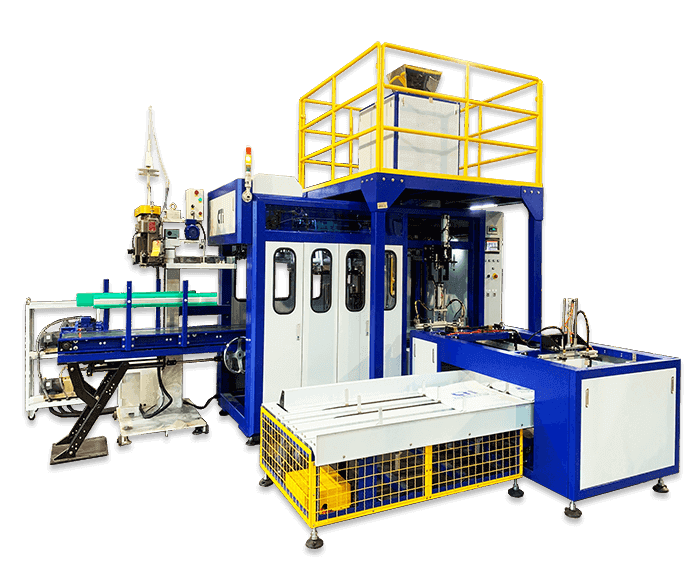
In a competitive manufacturing landscape, packaging is more than just a finishing step. It's a crucial part of the production line that affects efficiency, product quality, cost management, and compliance. Choosing the right packaging machine is not a one-size-fits-all decision—it requires careful evaluation of your production goals and operational needs. This guide outlines the main types of packaging equipment, the key factors to consider when making a selection, and practical tips to help your business make an informed investment.
Why Choosing the Right Packaging Machine Matters
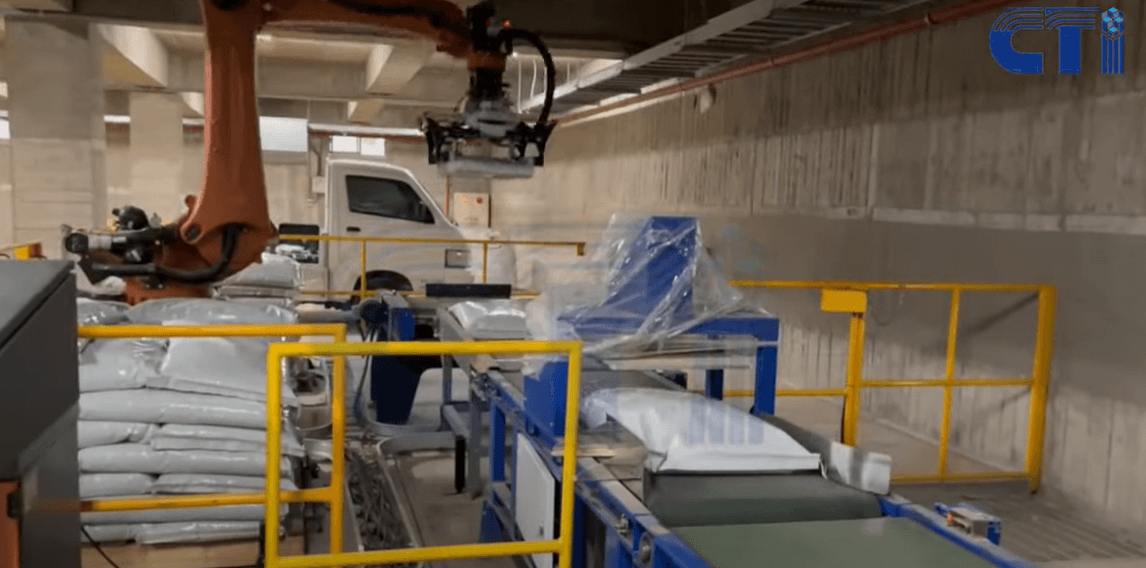
The correct packaging machine can greatly impact your production performance and bottom line. Here are four essential benefits:
- Boost Production Efficiency:
Require significant human intervention and are suitable for small-scale operations. - Ensure Packaging Quality and Consistency:
Maintaining consistent product appearance and integrity is vital for brand reputation. The right machines ensure precise, repeatable results with every cycle, reducing rework and customer complaints. - Minimize Material Waste:
By delivering precise measurements and flawless sealing, modern machines help reduce material waste and packaging errors—ultimately saving costs and supporting sustainability goals. - Comply with Market and Regulatory Demands:
The right machine helps you meet specific industry regulations (such as food safety or pharmaceutical GMP standards) more easily and reliably. Compliance also positions your product more favorably in regulated or export markets.
Overview of Common Packaging Machine Types
Let’s take a closer look at some of the most widely used packaging machines and the important roles they serve in today’s packaging operations.
- Filling Machines: Designed to dispense measured quantities of liquids, powders, or granules into containers. Suitable for food, beverages, chemicals, and more.
- Sealing Machines: Employ heat or vacuum technologies to seal packages securely. Common in food, pharmaceuticals, and electronics industries.
- Labeling Machines: Automatically apply labels to packages, enhancing branding and regulatory compliance.
- Shrink Wrapping Machines: Wrap products with heat-sensitive film that shrinks to form a tight seal. Often used for bundling and display packaging.
- Vacuum Packaging Machines: Remove air from packaging to extend product shelf life, particularly for perishable food items and sensitive electronics.
Key Factors to Consider When Choosing Packaging Equipment
Choosing a packaging machine involves far more than just selecting a model off the shelf. It's a strategic decision that impacts your production efficiency, cost structure, product quality, and long-term scalability. Below are six key factors every business should consider before investing:
1. Product Type and Characteristics
The physical properties of your product—whether it’s a liquid, solid, powder, viscous material, or fragile item—will determine the appropriate type of packaging equipment.
- Liquids (e.g., beverages, lotions): Best handled by flow or piston fillers, which provide precise volume control and prevent spills.
- Powders (e.g., spices, protein powder): Require auger fillers with dust-tight enclosures to maintain cleanliness and dosing accuracy.
- Fragile items (e.g., baked goods, sensitive electronics): Need gentle handling systems and soft-sealing mechanisms to avoid breakage or damage during packaging.
Each material has unique handling requirements, and selecting specialized technology ensures accurate filling, secure sealing, and minimal waste, ultimately protecting product integrity and brand reputation.
2. Production Volume and Capacity Needs
The scale and pace of your production line are key factors when selecting the right packaging machinery. Your equipment should not only meet current demand but also align with your business goals and future growth plans.
- Small-batch or custom production: For operations handling limited runs or frequent product changes, manual or semi-automatic machines offer greater flexibility and are more cost-effective in the short term. They allow for quick adjustments and are ideal when high-speed output isn't the top priority.
- High-volume or continuous production: If your business focuses on mass production, fully automatic systems are essential. These machines are designed for speed, consistency, and minimal human involvement, which leads to fewer errors, reduced labor costs, and higher output. They're especially valuable in sectors with tight delivery timelines or increasing demand.
Choose equipment that meets your current needs while allowing room for future expansion or integration to avoid unnecessary upgrades later.
3. Level of Automation
Evaluate how much automation your production line can support based on your budget, staffing, and operational goals:
- Manual systems: Lower cost but labor-intensive.
- Semi-automatic machines: Balance between control and efficiency.
- Fully automatic lines: High output with minimal manual input, ideal for high-volume manufacturing.
While fully automated systems require a higher upfront investment, they significantly reduce long-term labor costs and improve consistency.
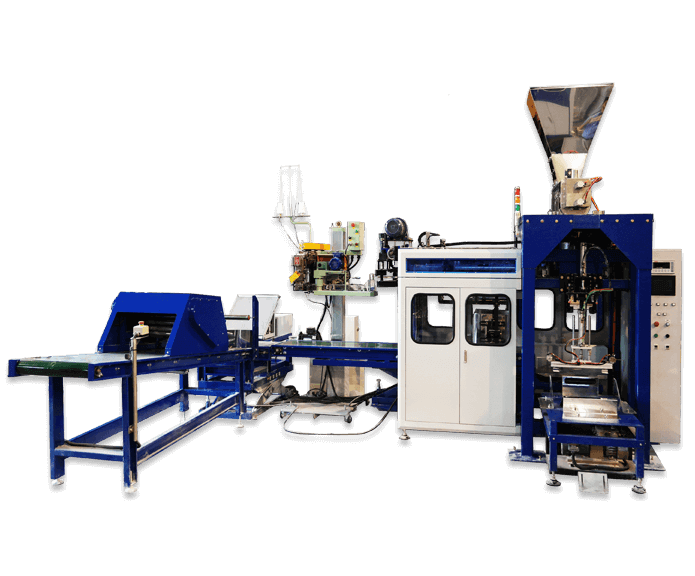
4. Compatibility and Flexibility
In today’s fast-changing market, packaging equipment must adapt quickly to variations in:
- Product size and weight
- Packaging materials (plastic, glass, aluminum, paper, etc.)
- Seasonal or promotional packaging formats
Look for machines that offer modular upgrades, fast tool-free changeovers, and programmable settings to accommodate multiple SKUs. Flexibility ensures long-term usability and better return on your investment.
5. Equipment Cost and Return on Investment (ROI)
Investing in packaging machinery involves more than just the upfront purchase price. A comprehensive cost analysis should include long-term factors such as:
- Energy efficiency: Machines with lower power consumption can significantly reduce ongoing utility costs.
- Maintenance and servicing: Consider ease of maintenance, availability of service personnel, and how frequently parts need replacement.
- Spare parts availability and cost: Choose machines with locally available, affordable components to minimize downtime.
- Operational efficiency: The ability to reduce packaging errors, boost throughput, and minimize labor directly contributes to long-term savings.
A higher upfront investment can often result in greater long-term value by improving productivity and lowering overall packaging costs.
6. After-Sales Service and Technical Support
Reliable technical support is critical for long-term performance. Partner with manufacturers or suppliers who offer:
- Prompt maintenance and repair services
- Ready availability of spare parts
- Local support teams
- Customized engineering assistance
CTI Machine is a trusted industry leader known for our strong after-sales support and tailor-made solutions for businesses of all sizes. Our service-oriented approach ensures minimal downtime and sustained operational excellence.
FAQ
Q1: With rising wages and labor shortages, how can I optimize my packaging line?
A: Introducing packaging machines can reduce operator workload and eliminate human-related errors, ensuring more consistent production.
Q2: How do I decide between semi-automatic and fully automatic packaging machines?
A: Semi-automatic machines are ideal for small businesses or startups with variable production needs. Fully automatic machines are better suited for high-volume production requiring minimal manual intervention.
Q3: Can one packaging machine handle multiple product types?
A: Some machines offer modular or adjustable features to handle a range of products. Always check with the supplier to ensure compatibility with your full product lineup.
CTI Machine: Comprehensive Packaging Systems for Every Step
Selecting the right packaging equipment requires more than just identifying a machine that works — it demands a thorough evaluation of your product characteristics, production volume, operational flexibility, and long-term budget planning. Every industry—from food and pharmaceuticals to agriculture and chemicals—has distinct requirements that call for specialized, efficient, and scalable solutions.
CTI Machine offers a full spectrum of advanced packaging machinery, including filling, sealing, and cartoning systems, as well as robotic palletizing arms that boost end-of-line automation and reduce manual handling. These intelligent systems are ideal for businesses aiming to optimize labor, improve safety, and scale production with ease.
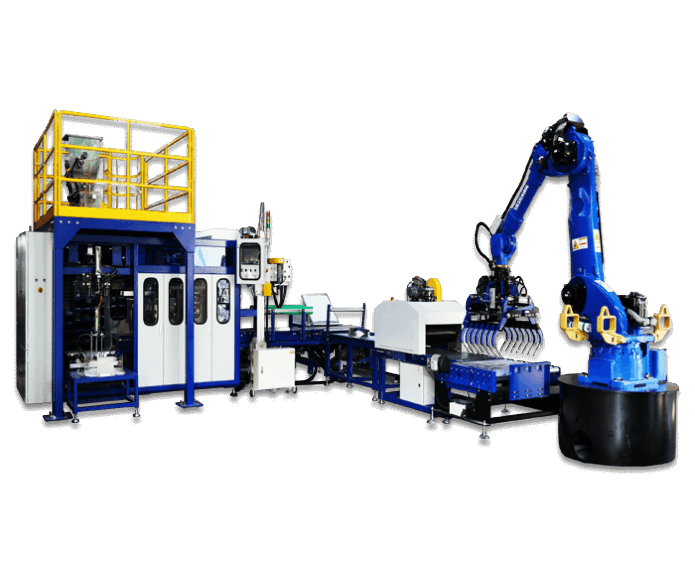
▲ Check out our Automatic Palletizing System
Not sure which machine fits your needs? Contact us today!